Valves
BALL VALVES
There are five general body styles of ball valves: single body, three piece body, split body, top entry, and welded. The difference is based on how the pieces of the valve-especially the casing that contains the ball itself-are manufactured and assembled. The valve operation is the same in each case.
In addition, there are different styles related to the bore of the ball mechanism itself:
- A full port or more commonly known full bore ball valve has an over-sized ball so that the hole in the ball is the same size as the pipeline resulting in lower friction loss. Flow is unrestricted but the valve is larger and more expensive so this is only used where free flow is required, for example in pipelines which require pigging.
- In reduced port or more commonly known reduced bore ball valves, flow through the valve is one pipe size smaller than the valve's pipe size resulting in flow area being smaller than pipe. As the flow discharge remains constant and is equal to area of flow (A) times velocity (V), A1V1 = A2V2 the velocity increases with reduced area of flow.
- A V port ball valve has either a 'v' shaped ball or a 'v' shaped seat. This allows the orifice to be opened and closed in a more controlled manner with a closer to linear flow characteristic. When the valve is in the closed position and opening is commenced the small end of the 'v' is opened first allowing stable flow control during this stage. This type of design requires a generally more robust construction due to higher velocities of the fluids, which might damage a standard valve.
- A trunnion ball valve has additional mechanical anchoring of the ball at the top and the bottom, suitable for larger and higher pressure valves (say, above 10 cm and 40 bars).
- Cavity filler Ball Valve. Many industries encounter problem with residues in the ball valve. Where the fluid is meant for human consumption, residues may also be health hazard, and when where the fluid changes from time to time contamination of one fluid with another may occur. Residues arise because in the half open position of the ball valve a gap is created between the ball bore and the body in which fluid can be trapped. To avoid the fluid getting into this cavity, the cavity has to be plugged, which can be done by extending the seats in such a manner that it is always in contact with the ball. This type of ball valve is known as Cavity Filler Ball Valve.
Manually operated ball valves can be closed quickly and thus there is a danger of water hammer. Some ball valves are equipped with an actuator that may be pneumatically or motor operated. These valves can be used either for on/off or flow control. A pneumatic flow control valve is also equipped with a positioner which transforms the control signal into actuator position and valve opening accordingly.
BUTTERFLY VALVES
A Butterfly Valve is a valve which can be used for isolating or regulating flow. The closing mechanism takes the form of a disk. Operation is similar to that of a ball valve, which allows for quick shut off. Butterfly valves are generally favored because they are lower in cost to other valve designs as well as being lighter in weight, meaning less support is required. The disc is positioned in the center of the pipe, passing through the disc is a rod connected to an actuator on the outside of the valve. Rotating the actuator turns the disc either parallel or perpendicular to the flow. Unlike a ball valve, the disc is always present within the flow, therefore a pressure drop is always induced in the flow, regardless of valve position.
A butterfly valve is from a family of valves called quarter-turn valves. The "butterfly" is a metal disc mounted on a rod. When the valve is closed, the disc is turned so that it completely blocks off the passageway. When the valve is fully open, the disc is rotated a quarter turn so that it allows an almost unrestricted passage of the fluid. The valve may also be opened incrementally to throttle flow.
There are different kinds of butterfly valves, each adapted for different pressures and different usage. The resilient butterfly valve, which uses the flexibility of rubber, has the lowest pressure rating. The high performance butterfly valve, used in slightly higher-pressure systems, features a slight offset in the way the disc is positioned, which increases the valve's sealing ability and decreases its tendency to wear. The valve best suited for high-pressure systems is the tricentric butterfly valve, which makes use of a metal seat,[ and is therefore able to withstand a greater amount of pressure.
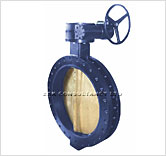
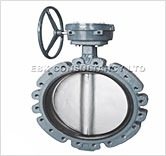
CHECK VALVES
Backwater Valve (for sanitary drainage system) protects lower located rooms against flooding caused by return flow of sewage waters. Such risk occurs most often in sanitary drainage systems connected to combined sewerage systems and in rainwater drainage systems. It may be caused by intense rainfall, thaw or flood. Backwater valve prevents rats and other rodents entering the sanitary and rainwater drainage systems and, consequently, the building interiors. It protects also against unpleasant smells in case of longer breaks in system use.
A Ball Check Valve is a check valve in which the closing member, the movable part to block the flow, is a spherical ball. In some ball check valves, the ball is spring-loaded to help keep it shut. For those designs without a spring, reverse flow is required to move the ball toward the seat and create a seal. The interior surface of the main seats of ball check valves are more or less conically-tapered to guide the ball into the seat and form a positive seal when stopping reverse flow.
Ball check valves are often very small, simple, and cheap. They are commonly used in liquid or gel minipump dispenser spigots, spray devices, some rubber bulbs for pumping air, etc., manual air pumps and some other pumps, and refillable dispensing syringes. Although the balls are most often made of metal, they can be made of other materials, or in some specialized cases out of artificial ruby. High pressure HPLC pumps and similar applications commonly use small inlet and outlet ball check valves with both balls and seats made of artificial ruby, for both hardness and chemical resistance. After prolonged use, such check valves can eventually wear out or the seat can develop a crack, requiring replacement. Therefore, such valves are made to be replaceable, sometimes placed in a small plastic body tightly-fitted inside a metal fitting which can withstand high pressure and which is screwed into the pump head.
There are similar check valves where the disc is not a ball, but some other shape, such as a poppet energized by a spring. Ball check valves should not be confused with ball valves, which is a different type of valve in which a ball acts as a controllable rotor to stop or direct flow.
A Diaphragm Check Valve uses a flexing rubber diaphragm positioned to create a normally-closed valve. Pressure on the upstream side must be greater than the pressure on the downstream side by a certain amount, known as the pressure differential, for the check valve to open allowing flow. Once positive pressure stops, the diaphragm automatically flexes back to its original closed position.[1]
A Swing Check Valve or Tilting Disc Check Valve is check valve in which the disc, the movable part to block the flow, swings on a hinge or trunnion, either onto the seat to block reverse flow or off the seat to allow forward flow. The seat opening cross-section may be perpendicular to the centerline between the two ports or at an angle. Although swing check valves can come in various sizes, large check valves are often swing check valves. The flapper valve in a flush-toilet mechanism is an example of this type of valve. Tank pressure holding it closed is overcome by manual lift of the flapper. It then remains open until the tank drains and the flapper falls due to gravity. Another variation of this mechanism is the clapper valve, used in applications such firefighting and fire life safety systems. A hinged gate only remains open in the inflowing direction. The clapper valve often also has a spring that keeps the gate shut when there is no forward pressure.
GATE VALVES
A Gate Valve, also known as a Sluice Valve, is a valve that opens by lifting a round or rectangular gate/wedge out of the path of the fluid. The distinct feature of a gate valve is the sealing surfaces between the gate and seats are planar, so gate valves are often used when a straight-line flow of fluid and minimum restric�tion is desired. The gate faces can form a wedge shape or they can be parallel. Typical gate valves should never be used for regulating flow, unless they are specifically designed for that purpose. On opening the gate valve, the flow path is enlarged in a highly nonlinear manner with respect to percent of opening. This means that flow rate does not change evenly with stem travel. Also, a partially open gate disk tends to vibrate from the fluid flow. Most of the flow change occurs near shutoff with a relatively high fluid velocity causing disk and seat wear and eventual leakage if used to regulate flow. Typical gate valves are designed to be fully opened or closed.[1] When fully open, the typical gate valve has no obstruction in the flow path, resulting in very low friction loss.[2]
Gate valves are characterised as having either a rising or a nonrising stem. Rising stems provide a visual indication of valve position because the stem is attached to the gate such that the gate and stem rise and lower together as the valve is operated. Nonrising stem valves may have a pointer threaded onto the upper end of the stem to indicate valve position, since the gate travels up or down the stem on the threads without raising or lowering the stem. Nonrising stems are used underground or where vertical space is limited.
Bonnets provide leakproof closure for the valve body. Gate valves may have a screw-in, union, or bolted bonnet. Screw-in bonnet is the simplest, offering a durable, pressure-tight seal. Union bonnet is suitable for applications requiring frequent inspection and cleaning. It also gives the body added strength. Bolted bonnet is used for larger valves and higher pressure applications.
Another type of bonnet construction in a gate valve is pressure seal bonnet. This construction is adopted for valves for high pressure service, typically in excess of 15 MPa (2250 psi). The unique feature about the pressure seal bonnet is that the body - bonnet joints seals improves as the internal pressure in the valve increases, compared to other constructions where the increase in internal pressure tends to create leaks in the body-bonnet joint.
Gate valves may have flanged ends which are drilled according to pipeline compatible flange dimensional standards. Gate valves are typically constructed from cast iron, ductile iron, cast carbon steel, gun metal, stainless steel, alloy steels, and forged steels.
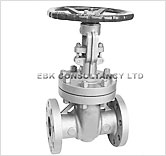
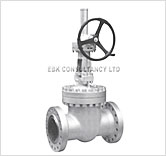
GLOBE VALVE
A Globe Valve is a type of valve used for regulating flow in a pipeline, consisting of a movable disk-type element and a stationary ring seat in a generally spherical body.[1]
Globe valves are named for their spherical body shape with the two halves of the body being separated by an internal baffle. This has an opening that forms a seat onto which a movable plug[2] can be screwed in to close (or shut) the valve. The plug is also called a disc or disk.[3][4] In globe valves, the plug is connected to a stem which is operated by screw action in manual valves. Typically, automated valves use sliding stems. Automated globe valves have a smooth stem rather than threaded and are opened and closed by an actuator assembly. When a globe valve is manually operated, the stem is turned by a handwheel.
Although globe valves in the past had the spherical bodies which gave them their name, many modern globe valves do not have much of a spherical shape. However, the term globe valve is still often used for valves that have such an internal mechanism. In plumbing, valves with such a mechanism are also often called stop valves since they don't have the global appearance, but the term stop valve may refer to valves which are used to stop flow even when they have other mechanisms or designs.
Globe valves are used for applications requiring throttling and frequent operation. For example, globe valves or valves with a similar mechanism may be used as sampling valves, which are normally shut except when liquid samples are being taken. Since the baffle restricts flow, they're not recommended where full, unobstructed flow is required.
NEEDLE VALVE
A Needle Valve has a relatively small orifice with a long, tapered seat, and a needle-shaped plunger, on the end of a screw, which exactly fits this seat.
As the screw is turned and the plunger retracted, flow between the seat and the plunger is possible; however, until the plunger is completely retracted the fluid flow is significantly impeded. Since it takes many turns of the fine-threaded screw to retract the plunger, precise regulation of the flow rate is possible.
The virtue of the needle valve is from the vernier effect of the ratio between the needle's length and its diameter, or the difference in diameter between needle and seat. A long travel axially (the control input) makes for a very small and precise change radially (affecting the resultant flow).
Needle valves are usually used in flow metering applications, especially when a constant, calibrated, low flow rate must be maintained for some time, such as the idle fuel flow in a carburetor.
Note that the float valve of a carburetor (controlling the fuel level within the carburetor) is not a needle valve, although it is commonly described as one. It uses a bluntly conical needle, but it seats against a square-edged seat rather than a matching cone. The intention here is to obtain a well-defined seat between two narrow mating surfaces, giving firm shutoff of the flow from only a light float pressure.
Since flow rates are low and many turns of the valve stem are required to completely open or close, needle valves are not used for simple shutoff applications.
Since the orifice is small and the force advantage of the fine-threaded stem is high, needle valves are usually easy to shut off completely, with merely "finger tight" pressure. Small, simple needle valves are often used as bleed valves in hot water heating applications.
Unlike a ball valve, or valves with a rising stem, it is not easy to tell from examining the handle position whether the valve is open or closed.